بهترین کار این است که انتخاب نوار نقاله مناسب به یک متخصص مشغول به کار در شرکت سازنده نوار نقاله یا توزیع کننده یا مشاور مستقل واگذار شود. نوار نقاله درست انتخاب شده و ساخته شده بهترین عملکرد و عمر را با حداقل هزینه دارد.
انتخاب یا جایگزینی نامناسب نوار نقاله می تواند نتایج فاجعه آمیزی داشته باشد. در ادامه این مقاله به بررسی مشخصات نوار نقاله و شناخت بهتر ساختمان نوار نقاله می پردازیم.
انتخاب نوار نقاله مناسب
تعدادی پارامتر کاری و شرایط مواد وجود دارد که باید هنگام انتخاب نوار نقاله مناسب، جزئیات آن مشخص شود. در ادامه به شرح جزییات انتخاب نوار نقاله مناسب می پردازیم.
ضخامت
تلرانس %20+/- برای روکش های نازک مثل 2.4 mm یا 0.094 in و %5+/- برای روکش های ضخیم تر از 19 mm یا 0.75 in
خمیدگی یا قوس camber or bow
خمیدگی یا قوس را به یک چهارم یک درصد 0.0025 محدود کنید. یعنی 25 mm+/- در 10 m یا 0.75 in در 25 ft . خمیدگی لبه محدب نوار نقاله و قوس لبه مقعر نوار نقاله است. آر.اِم.اِ قوس یا خمیدگی را به عنوان نسبت فاصله وسط بین دو نقطه واقعی روی نوار نقاله با فاصله 15-30 m یا 50-100 ft و خط مستقیم بین آن دو تعریف می کند.
برای نوشتن آن به درصد، مقدار اعشاری به دست آمده را در 100 ضرب کنید. برای مثال اگر30 m نوار نقاله به اندازه 450 mm یا 0.45 m انحراف داشته باشد، معادل قوس 1.5 % است. در مقیاس اینچی معادل انحنای 18 in یا 1.5 ft در طول 100 ft برابر 1.5 % خواهد شد.
سطح نوار
سطح نوار نقاله باید صاف ، تخت و سختی یکنواخت در محدوده 5+/- واحد باشد. سختی لاستیک در آمریکا با واحد Shore A Durometer (دورومتر) اندازه گیری می شود. محدوده آن بین 30 تا 95 است و هرچه عدد بیشتر باشد، سختی بیشتر است. درجه سختی بین المللی لاستیک (IRHD) محدوده 0-100 دارد که اشاره به مدول الاستیک برابر 0 و بی نهایت 100 دارد.
آرم سازنده
از سازنده بخواهید آرم خود را حذف کند یا روی روکش زیرین حک کند تا با تمیزکن نقاله و سیستم های درزبندی تداخل نداشته باشد. جزئیات شرایط کاری هنگام تعیین نوار نقاله عبارت است از:
- تعداد ساعت کاری بارگیری و تخلیه
- جزییات نقطه انتقال شامل زاویه تغار و فاصله تغییر شکل و اطلاعاتی از مسیر مواد، ارتفاع ریزش و سرعت
- شرح حتی الامکان کامل مواد بالک شامل اندازه ذرات و دمای مواد
- شرح سیستم تمیزکن بکار رفته
- شرح مواد شیمیایی بکار رفته (مثل ضدیخ و غبارنشان)
- شرح آلاینده های جوی (از فرایندهای همجوار یا دیگر منابع)
- تعیین بدترین وضعیت آب و هوایی که نوار نقاله باید تحمل کند.
شناخت ساختمان نوار نقاله مناسب
گذاشتن هر نواری روی ساختمان یک کانوایر بدون شناخت مشخصات نوار نقاله، عملکرد سیستم را مختل خواهد کرد و عملکرد نوار نقاله را کاهش خواهد داد. ممکن است مشکلاتی در انحراف نوار، کوتاه شدن عمر، اتصالات آسیب دیده، توقف های خارج از برنامه و افزایش هزینه های تعمیرات را به دنبال داشته باشد.
یک تحلیل تفصیلی ساختمان نوار نقاله مناسب و اجزای رولیک موردنیاز است تا از انتخاب نوار نقاله مناسب اطمینان حاصل شود. توصیه می شود همه پارامترها قبل از انتخاب و نصب نوار نقاله مناسب روی یک کانوایر موجود بررسی شوند. عاقلانه است که توصیه های سازنده نوار نقاله درنظرگرفته شود.
سازگاری با ساختمان و اجزای دورانی
خریدن نوار نقاله مثل خریدن لباس است. برای بهترین تناسب باید به اندازه کانوایر موجود دوخته شود. نوارهای نقاله با ظرفیت، طول، عرض، زاویه تغاری و کشش های مختلف طراحی می شوند. یک نوار نقاله مناسب باید با ساختمان کانوایر مطابقت داشته باشد و مسئله چیزی بیش از فقط عرض نوار نقاله است.
متأسفانه اغلب این مسئله در سطح عملیاتی یک کارخانه موردتوجه قرار داده نمی شود. اغلب گفته می شود نوار، نوار است. این از عدم دانستن پیچیدگی روابط نشات می گیرد. معمولا وقتی می خواهند به سرعت کانوایر را راه اندازی کنند یا مشکل را اقتصادی حل کنند این فلسفه عملی می شود. پاسخ معمول در این شرایط استفاده از نوار نقاله موجودی انبار یا نوار نقاله موجود در منابع بیرونی مثل پخش کننده نوار است.
استفاده از نوار نقاله مقرون به صرفه که کاملا مطابق با سیستم کانوایر نیست، کار اقتصادی غلطی است. عدم تطابق نوار نقاله با ساختمان، مسئله مشهور عملکرد ضعیف نوار نقاله و برگشت سرمایه آن است. این عدم تطابق می تواند مشهورترین علت انحراف نوار نقاله بخاطر تعویض نوار نقاله یا اضافه کردن تکه ای به نوار نقاله موجود باشد. درک اصول انطباق برای عملکرد خوب نوار نقاله و کانوایر ضروری است.
مشخص کردن یک نوار نقاله وظیفه مهمی است. بهترین کار این است که واحد تولید، مسئولیت انتخاب نوار نقاله مناسب را به یک متخصص واگذار کند. این متخصص با قابلیت های کانوایر آشنا خواهد شد و سؤالات درستی را خواهد پرسید.
درجه بندی کشش نوار نقاله مناسب
هر نوار نقاله برحسب استحکام آن (مقدار نیروی کششی که می تواند تحمل کند) درجه بندی rating می شود. استحکام یک نوار نقاله (یا دقیق تر کششی که می تواند تحمل کند) در آمریکا بر حسب پوند بر اینچ عرض نوار نقاله با مختصر معمول PIW درجه بندی می شود. در بقیه نقاط دنیا نوار نقاله بر اساس استحکام شکست نهایی بر حسب ابعاد متریک نیوتن بر میلیمتر N/mm یا کیلونیوتن بر متر kN/m درجه بندی می شود.
درجه بندی استحکام تابعی از تقویتی شامل اسکلت نوار نقاله و تعداد و نوع و جنس پارچه ها یا اگر نوار نقاله کابل فولادی باشد اندازه کابل ها است. همانطور که قبلا گفته شد روکش های فوقانی و زیرین نوار نقاله تاثیر بسیار کمی روی استحکام نوار نقاله یا درجه کشش دارند.
استحکام نوار نقاله، میزان کشش اسکلت یا استحکام شکست نهایی، نشان دهنده مقدار نیرویی است که می توان به نوار نقاله اعمال کرد. وارد کردن نیروی بیشتر از طریق بار مواد، وزنه کشش و جاذبه شیب می تواند باعث پاره شدن نوار نقاله شود. هرچه نرخ کشش نوار نقاله بیشتر باشد، تطابق آن با سازه و اجزای دورانی بحرانی تر می شود.
هر سازه کانوایر، یک نوار نقاله مناسب با نرخ کشش خاصی لازم دارد. فاکتورهای تأثیرگذار عبارت است از:
- طول سازه
- زاویه شیب کانوایر
- ظرفیت مورد نیاز
- عرض نوار
- نیروی کشش و اینرسی اجزای دورانی
حداقل شعاع خم
نوار نقاله با حداقل اندازه پولی بر اساس مشخصات سازنده طراحی می شود. خم کردن یک نوار نقاله به دور یک شعاع خیلی کوچک می تواند نوار نقاله را خراب کند. این کار ممکن است باعث از هم باز شدن یا خرابی پارچه ها یا ترک خوردن روکش فوقانی شود. همچنین اندازه کوچک پولی می تواند باعث باز شدن اتصالات مکانیکی نوار نقاله شود. حداقل قطر پولی با تعداد و جنس لایه ها، چه فولادی و چه پارچه ای، نرخ کشش نوار نقاله و ضخامت روکش فوقانی و زیرین تعیین می شود.
هنگام طراحی یک سیستم جدید ممکن است تمایل به استفاده از نوار ضخیم تر برای افزایش عمر نوار در سایش و ضربه نیاز به نصب پولی بزرگتر ایجاد کند.
یک اشتباه معمول وقتی اتفاق می افتد که در یک عملیات متوجه خرابی سطح حمل بار نوار می شوند. اولین اقدام استفاده از نوار ضخیم تر با طول عمر بیشتر است. اگر به ازای نوار ضخیم تر، حداقل قطر پولی موردنیاز آن بزرگتر از قطر پولی موجود باشد، ممکن است عمر نوار کمتر شده و بجای حل مشکل شرایط را بدتر کند.
زاویه تغاری
نوارها به شکل تغار درمی آیند تا بار بیشتری را حمل کنند. با افزایش زاویه تغاری مواد بیشتری می توان حمل کرد. همه نوارهای پی.وی.سی یا لاستیک تخت می توانند به شکل تغاری دربیاید. نوع اسکلت نوار، ضخامت نوار، عرض نوار و نرخ کشش نوار حداکثر زاویه تغاری را تعیین می کند. در مشخصات فنی سازنده نوار نقاله معمولا حداقل عرض نوار برای زاویه های تغاری مختلف داده می شود.
تجاوز از حداکثر زاویه تغاری یک نوار می تواند باعث شود که نوار همیشه به حال کاسه ای تغییر شکل بدهد. کاسه ای شدن نوار می تواند درزبندی و تمیز کردن آن را مشکل نماید و مسیریابی آن را غیرممکن نماید. با افزایش کاسه ای شدن سطح تماس کانوایر با رولیک ها کاهش یافته و در نتیجه توانایی رولیک ها در هدایت نوار کاهش می یابد.
اگر از قابلیت تغاری شدن نوار فراتر روید، ممکن است نوار به درستی شکل تغاری به خود نگیرد، مشکلات درزبندی و مسیریابی بوجود آید. اگر نوار خیلی سفت باشد، بطور مناسب به شکل تغار درنمی آید و توسط سیستم به خوبی هدایت نمی شود.
این وضعیت به سرعت ریزش بار از لبه های نوار و خرابی لبه نوار را به دنبال دارد. در صورت تغاری کردن نوار بیش از حد مجاز، مشکل دیگری که ممکن است اتفاق بیافتد خرابی روکش های بالا و پایین و اسکلت در محل اتصال رولیک ها است. برای کسب اطلاعات بیشتر می توانید به مقاله تعمیرات، نگهداری رولیک ها مراجعه نمایید.
در ضمن اگر قابلیت تغاری شدن نوار با زاویه رولیک ها مطابقت نداشته باشد، ممکن است توان بیشتری برای به حرکت کانوایر نیاز باشد.
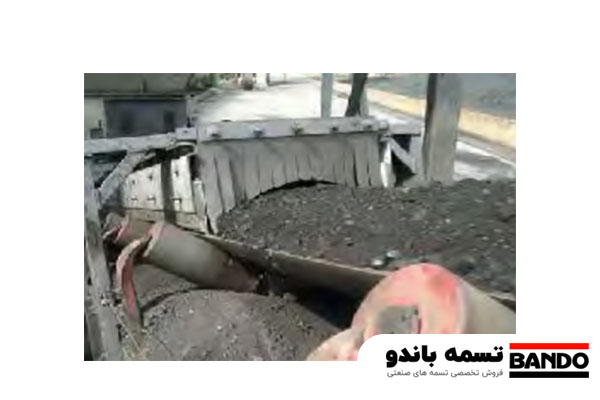
فاصله گذار
نوار در حالت تخت از روی پولی انتها عبور می کند. پس از اینکه نوار پولی انتها را ترک کرد و وارد ناحیه بارگیری شد، لبه های نوار نقاله بالا می رود و در محل بارگیری شکل تغاری به خود می گیرد. این تغار با رولیک های گذار، رولیک هایی که زاویه آنها بین تخت و زاویه نهایی تغار می باشد، شکل می گیرد.
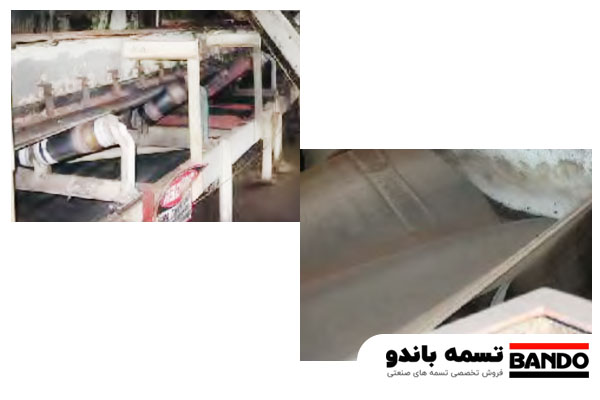
مشابه همین منطقه گذار ولی بالعکس در سر پولی اتفاق می افتد. در آنجا نوار نقاله شکل تغاری دارد و باید قبل از رسیدن به نقطه تخلیه شکل تخت بیابد.
وقتیکه نوار نقاله به شکل تغاری در می آید، لبه های بیرونی بیشتر از وسط نوار نقاله کشیده می شود. اگر گذار در فاصله کوتاهی انجام شود، ممکن است نوار نقاله در ناحیه اتصال رولیک دچار آسیب شود، نقاط تقاطع رولیک تخت و رولیک های جناحین.
دیدن کانوایری که فاصله گذار آن کوتاه است، عادی است. دلایل مختلفی برای این وجود دارد. مهندسی غلط یا عدم فهم اهمیت گذار، فضای کم یا تمایل به کاهش هزینه ها. بنابراین بسیار حیاتی است که با استفاده از نواری که فاصله گذار بیشتری نیاز دارد، مشکل را بیشتر نکنیم.
ممکن است بتوان فاصله گذار یک کانوایر را افزایش داد. دو راه برای این کار وجود دارد. یک روش این است که پولی انتها به عقب برده شود تا فاصله قبل از ناحیه بارگیری افزایش یابد. روش دوم جور کردن دو ناحیه گذار است، که نوار نقاله قبل از ورود به ناحیه بارگیری کمی حالت تغاری به خود بگیرد و پس از بارگیری به شکل کاملا تغاری دربیاید.
اما در بیشتر شرایط بخاطر کمبود فضا و بودجه مانع افزایش فاصله گذار می شوند. شایع ترین راه حل، اطمینان از انتخاب مناسب نوار نقاله برای فاصله گذار موجود است. با توجه به همه هزینه ها مثل مشکلات بارگیری، افزایش کشش لبه و خرابی نوار نقاله ممکن است این، بهترین راه حل اقتصادی نباشد. طراحی ضعیف ناحیه گذار، هزینه ها را افزایش داده و عمر نوار نقاله را کاهش می دهد.
منبع: کتاب FOUNDATIONS ترجمه معصومه امین.