در این مقاله قصد داریم به شرح مفصل تر نکات مهم در طراحی شوت های انتقال در نوار نقاله ها بپردازیم. بنابراین در ادامه مقاله به شرح ملاحظات طراحی شوت های انتقال، مدیریت سایش و جریان مواد، بارگیری نوار دریافت کننده، مدیریت جریان هوا، بدنه شوت و مباحث پیشرفته خواهیم پرداخت.
برای کسب اطلاعات بیشتر برای خرید انواع قطعات و چسب های نوار نقاله ها می توانید با بازرگانی تسمه باندو تماس بگیرید.
ملاحظات طراحی شوت های انتقال
حجم شوت سر (تخلیه) در اطراف پولی کانوایر اغلب توسط چیدمان کلی کانوایرها، الزامات دسترسی برای تعمیرات، و مسیر اولیه مواد دیکته می شود. عرض و قطر پولی سر head به تعیین عرض و ارتفاع شوت سر کمک می کند.
فضای بین دیواره شوت و لبه پولی باید به قدر کافی کم باشد تا مواد درشت مسیر رفت نتواند به مسیر برگشت بریزد و بین پولی و دیواره شوت گیر نکند. فضای معمول 50-75 mm یا 2-3 in در هر طرف است. تعمیر پولی و روکش آن و دسترسی به بوش های شفت در هنگام تعیین این فاصله باید درنظرگرفته شود.
شوت سر باید از آخرین رولیک کاملا تغاری نوار تحویل دهنده شروع شود تا هنگام تغییر شکل نوار از تغاری به تخت روی پولی هد، به محدود کردن هرگونه مواد نشتی کمک کند. سطح ورودی شوت سر head chute باید با پرده های غبار dust curtain روی مسیر رفت و موانع درزبندی barrier seal در مسیر برگشت کنترل شود، چون این مناطق عوامل کلیدی در جریان هوا داخل شوت می باشند.
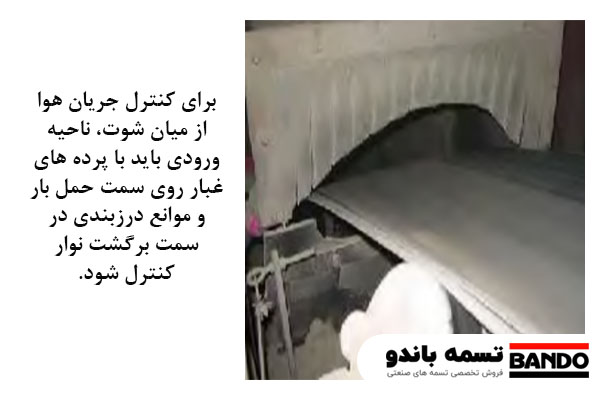
بعد از اینکه مواد در اولین برخورد با بدنه شوت سر تغییر جهت دادند، اغلب به سمت شوت انتقال یا ریزش drop (transition) هدایت می شوند. این شوت های انتقال می توانند شبیه داکت، جریان مواد را با تنظیم درست روی نوار دریافت کننده تحویل دهند.
لازم است همه این شوت های انتقال به اندازه کافی شیبدار باشند تا مانع چسبیدن مواد به دیواره های آن شوند. همچنین باید به اندازه کافی بزرگ باشند تا از گرفتگی جلوگیری کنند.
معمولا پذیرفته شده است که سطح مقطع شوت های انتقال حداقل 4 برابر سطح مقطع جریان مواد باشد. همچنین معمولا پذیرفته شده است که عرض و عمق حداقل 2.5 برابر بزرگترین اندازه ذرات که احتمال می رود از شوت عبور کند، باشد.
بسیاری از طراحان بر اساس تجربه خودشان برای مواد خاص این ضرایب را افزایش می دهند. در برخی شرایط که اندازه ذرات مواد بالک یکنواخت است و به آزادی جریان می یابد، می توان این ضرایب را کاهش داد، مخصوصا وقتی شوت انتقال با استفاده از خواص تعیین شده مواد بالک، مهندسی شده است.
عرض شوت بارگیری loading (دریافت کننده) باید بگونه ای در طراحی شوت درنظر گرفته شود که حداقل لبه برای درزبندی و انحراف نوار خالی بگذارد.
مشهورترین اشتباه در این مرحله، انتقال ناگهانی از شوت انتقال یا ریزش به شوت بارگیری است، زوایایی در شوت بوجود می آید که مواد در آن جمع شده و گرفتگی بوجود می آید. در طراحی شوت های جدید، زاویه کنج شوت حداقل 60 درجه و ترجیحا 75 درجه لحاظ می شود.
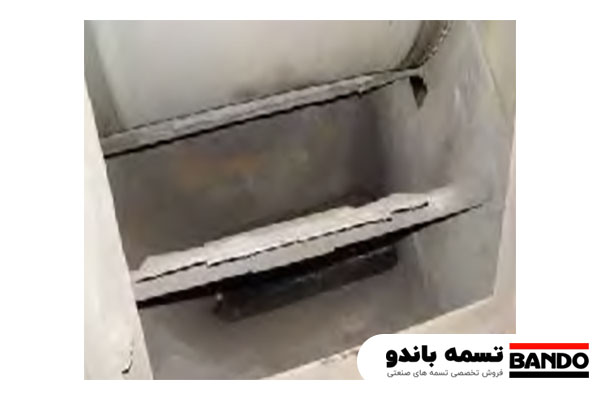
مدیریت سایش و جریان مواد در شوت های انتقال
طراحی شوت انتقال غالبا برای جریان کامل و یک مسیر پایدار مواد انجام می شود. اما جریان مواد با تغییر خواص مواد، تغییر دبی مواد، سایش شوت های انتقال، یا تجمع مواد روی دیواره شوت تغییر خواهد کرد.
منحرف کننده ها
منحرف کننده deflector ممکن است در داخل شوت های انتقال برای جذب ضربه و حداقل نمودن سایش بکار رود، از نقطه ای که مسیر مواد با شوت سر برخورد می کند، شروع می شود. مهم است که فاصله بین منحرف کننده و پولی تخلیه سر کانوایر به اندازه کافی باشد تا از مسدود کردن محل عبور مواد توسط سنگ های درشت یا چسبیدن مواد با پیوستگی زیاد به صفحه جلوگیری کند، که در غیر اینصورت می تواند باعث گرفتگی شوت شود.
وقتی مواد اولین نقطه برخورد با شوت، را ترک می کنند، ممکن است لازم باشد که جریان مواد در ابتدای سیستم کمی تنظیم شود. منحرف کننده ها یا صفحات ضربه زن kicker plate اغلب در طرح اولیه وجود دارد یا در راه اندازی نصب می شود تا جریان مواد را هدایت کند.
هنگام راه اندازی یک کانوایر جدید، معمول است که منحرف کننده هایی داخل شوت نصب می شود تا به مرکز شدن جریان مواد کمک کند. فرایند بدست آوردن جریان موردنظر اغلب سعی و خطاست. این صفحات منحرف کننده باید قابل تنظیم باشند تا بتوان برای بدست آوردن اثر مطلوب آن را تغییرمکان داد. محل های دسترسی و بازرسی برای رویت و ایجاد جهت مناسب منحرف کننده ها ضروری است.
هدایت بار ممکن است با گذاشتن منحرف کننده داخل شوت بارگیری، برای جهت دادن بار به مرکز ناحیه بارگیری بهتر شود. موادی که به مرکز هدایت شده اند، احتمال کمتری دارد که به سمت لبه های نوار بلغزد یا درزبندی اسکرت را خراب کند.
لاینرهای سایشی منحرف کننده پایین شوت بارگیری نزدیک نوار، می تواند مشکلات ریزش بار خارج از مرکز را کاهش دهد. یک یا چند منحرف کننده یا صفحات ضربه زن ممکن است لازم باشد تا مواد را به مسیر مناسب تغییر جهت دهد و بار را در مرکز نوار بریزد. این لاینرها به شکل خم یا زاویه دار هستند که مواد را به سمت مرکز نوار و به دور از لبه ها برمی گردانند. لاینرهای سایشی دلفکتور باید به دقت بکار روند، چون ممکن است مشکلات دیگری ایجاد کنند، مثل گیرافتادن مواد و خفه شدن chocking شوت.
روش مشهور برای مدیریت مواد بالک در شوت و حداقل کردن برخورد، نصب میله های سرندی scalping bars یا بستر بار مرده rock box است.
میله های سرندی یا گریزلی
میله های سرندی، که گریزلی یا میله گریزلی نیز گفته می شود، در داخل شوت، مواد ریز را عبور داده و یک بستر نرم روی نوار تشکیل می دهد. سنگ های درشت از بین میله ها عبور نکرده، به سمت پایین سُر خورده و روی بستر نرم نوار که قبلا توسط مواد ریزدانه تشکیل شده، می نشینند. اغلب کارخانه ها در محل تخلیه بار از کامیون، از گریزلی مثل یک شبکه استفاده می کنند، تا مانع ورود مواد درشت تر از حد مجاز به سیستم شود.
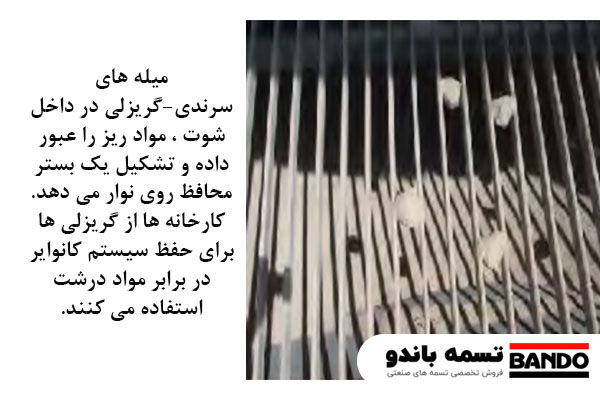
بستر بار مرده
بستر بار مرده یک طاقچه داخل شوت انتقال است که توده ای از مواد آنجا جمع می شود. مواد بعدی از روی این مواد جمع شده عبور می کند. نیروی سایش از دیواره به بستر بار مرده منتقل می شود، و ارتفاع ریزش بطور کلی کاهش می یابد و انرژی مواد در برخورد با بستر بار مرده تلف می شود.
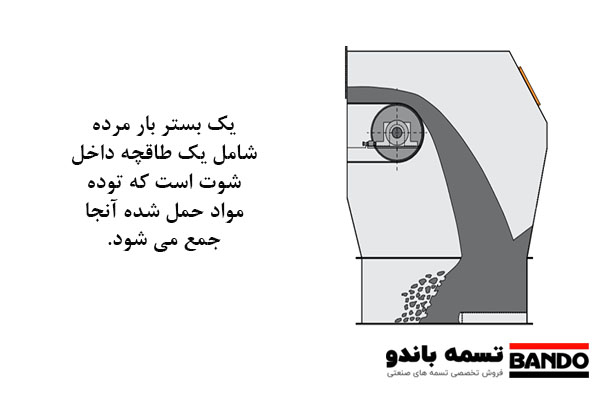
نردبان های سنگی rock ladder که از یک سری موانع یا بستر بار مرده های کوچک تشکیل شده است، برای کاهش ضربه و کنترل سرعت مواد هنگام ریزش از ارتفاع زیاد به کار می رود. نردبان های سنگی معمولا به طور متناوب در طرفین شوت به گونه ای نصب می شوند که ارتفاع سقوط آزاد مواد هیچوقت از 1.5-2 m یا 5-6 ft بیشتر نمی شود.
بستر بار مرده و نردبان های سنگی برای حمل موادی مثل شن و ماسه و سنگ های سخت بسیار مناسب است. بهترین شرایط کاری بستر بار مرده، ثابت ماندن شرایط فیزیکی و دبی مواد است، چون مهم است که جریان مواد بطور پایدار از روی بستر بار مرده عبور کند. باید توجه شود که قضاوت درستی در مورد پیوستگی مواد (مثلا تحت شرایط رطوبتی) انجام شود تا از جمع شدن مواد و منجر شدن به گرفتگی شوت، اجتناب شود. بسترهای بار مرده نباید برای مواد شکننده (بخاطر کاهش کیفیت) یا مواد خیلی درشت که می تواند جریان مواد را مسدود کند، استفاده شود و برای کانوایری که مواد مختلف حمل می کند نیز نباید استفاده شود.
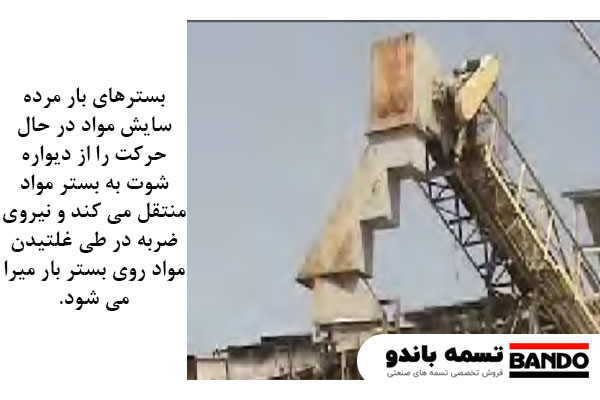
صفحات یا شبکه های ضربه گیر
روش دیگر برای تغییر جهت مواد و جذب ضربه داخل شوت، استفاده از صفحات ضربه گیر یا شبکه در مسیر جریان مواد می باشد. صفحه ضربه گیر در داخل شوت جاسازی می شود تا نیروی جریان مواد در حال حرکت را جذب کند. صفحات ضربه گیر اغلب در انتقال های زاویه دار کاربرد دارد که سرعت نوار زیاد است و موقعیت (مثل فضا و بودجه موجود) مانع مهندسی شوت وسیع و مفصل است.
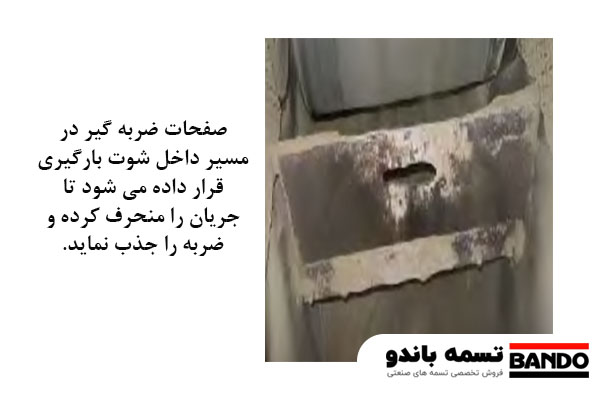
برخی شبکه های ضربه گیر برای گرفتن مواد و گسترش ضربه مواد به مواد و محافظت از دیواره شوت بکار می روند. مواد بعدی روی مواد گیرکرده در شبکه می غلتد بدون اینکه در واقع با شبکه یا دیواره برخورد داشته باشد. فاصله بین پولی سر تا صفحه ضربه گیر باید به دقت انتخاب شود تا مشکل گیرکردن مواد بزرگ یا قراضه بین پولی و صفحه یا تجمع مواد با پیوستگی بالا یا مرطوب بوجود نیاید، وگرنه ممکن است باعث گرفتگی شوت شود.
انتخاب مواد مناسب و توجه دقیق به طراحی شوت به طور درست و جانمایی این صفحات و شبکه های ضربه گیر، می تواند به مقدار زیادی عمر این اجزای سایشی را بالا ببرد.
لاینر های ضد سایش
برخورد مداوم و سُر خوردن مواد روی دیواره های شوت مهمترین عامل سایش یک شوت می باشد. علاوه بر شبکه ها، بستر بار مرده و صفحات ضربه گیر که توضیح داده شد، یک روش کاهش سایش، استفاده از لاینرهای فداشونده داخل شوت است. ممکن است لاینر برای کاهش اصطکاک دیواره و یا چسبندگی مواد نیز استفاده شود. در انتخاب یک ماده به عنوان لاینر، هدف انتخاب ماده ای است که هم مقاوم در برابر سایش باشد و هم جریان مواد را بهبود دهد.
بارگیری نوار دریافت کننده
پدیده دیگری که در نقاط انتقال اتفاق می افتد ریزش عمودی مواد روی نوار با سرعت بالاست که انباشت مواد pooling گفته می شود. موادی که هنوز با نوار نقاله هم سرعت نشده اند. روی نوار نقاله جمع شده و یک استخر مواد روی ناحیه بارگیری تشکیل می دهند.
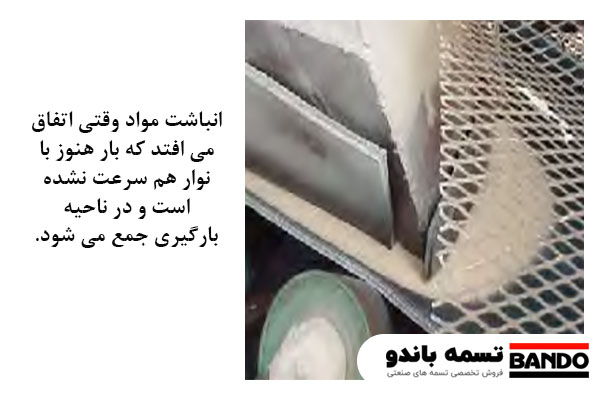
وقتی یک سنگ با نوار برخورد می کند، به این طرف و آن طرف می پرد تا انرژی نوار قبل و سقوط آزاد را تلف کند و با نوار دریافت کننده هم سرعت شود. در این بین، مواد می تواند از توده مواد به طرفین یا پشت کانوایر غلت بخورد و ریزش مواد را موجب شود.
هرچه اختلاف سرعت بین جریان مواد و نوار دریافت کننده بیشتر باشد، انباشت مواد طولانی تر و عمیق تر خواهد بود. هرچه این انباشت مواد گسترش یابد، کنترل درزبندی، ریزش مواد و سایش روکش نوار نقاله مشکل تر خواهد شد.
یک کانوایر سرعت بالا برای جبران این شرایط می تواند به کار رود. راه دیگر استفاده از یک دریچه منحنی، سطح شیبدار، یا چمچه برای کنترل سرعت و جهت جریان مواد است تا به سرعت و جهت نوار دریافت کننده برسد.
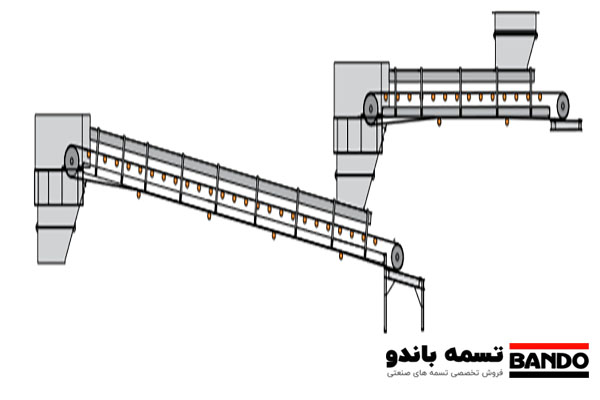
این شوت های بارگیری منحنی جریان مواد را هدایت کرده، به مرکز نوار دریافت کننده می ریزند. هرچه قراردادن بار روی کانوایر دریافت کننده نرم تر باشد، حرکت مواد به لبه های نوار کمتر خواهد بود، انرژی کمتری آزاد کرده و غبار به حداقل می رسد.
زاویه ای که شوت از کانوایر تخلیه به سمت نوار دریافت کننده سرازیر می شود، باید به اندازه کافی تخت باشد تا مانع غلت خوردن بیش از حد مواد روی نوار شود. یک شوت با حداقل زاویه کنج ممکن، به همراه جهت و سرعت مناسب بار، اجازه می دهد مواد با زاویه تغذیه با نوار برخورد کند.
در این صورت مواد همچنان که در جهت نوار حمل می شود، به آرامی روی نوار غلت می خورد، بجای اینکه به سمت عقب و جریان مواد ورودی برخورد کند. یک شوت منحنی خطر خرابی نوار و کاهش کیفیت مواد و تولید غبار را کاهش می دهد.
اما باید توجه داشت که اگر زاویه شوت خیلی تخت باشد، ممکن است جریان مواد آنقدر آهسته شود که متوقف شده، جمع شده و در نهایت باعث گرفتگی شوت شود. معمولا زاویه کنج برای طراحی شوت های مرسوم بین 60 الی 75 درجه از خط نوار دریافت کننده است.
مدیریت جریان هوا در طراحی شوت ها
طراحی شوت به طور درست می تواند بطور عمده غبار را با محدود کردن جریان هوا کاهش دهد. مقطع اسکرت باید به اندازه کافی بزرگ باشد تا محفظه ای را بوجود آورد که جریان هوا را آرام نموده و فشار مثبتی که می تواند ذرات غبار را به بیرون محفظه حمل کند، کاهش دهد.
محفظه باید به اندازه کافی بزرگ باشد تا یک کاهش عمده در سرعت هوا بوجود آورده و بنابراین اجازه دهد ذرات شناور در هوا قبل از خروج کانوایر از محفظه به روی بار ته نشین شود.
بدنه شوت
شوت معمولا از ورق های فولادی یا ضد زنگ ساخته می شود که انتخاب جنس بر حسب نوع مواد و امکانات انجام می شود. انتخاب ضخامت ورق بدنه شوت بستگی دارد به مشخصات و حجم مواد عبوری از شوت، الزامات استحکام ساختمانی، و مقدار سایش در صورتیکه شوت لاینر قابل تعویض نداشته باشد.
قوانین محلی معمولا طراحی شوت را کنترل می کنند، اما این وظیفه طراح است که همه بارهای وارده به شوت را درنظر بگیرد. برخی بارهای مهمتر عبارت است از وزن شوت، تجمع مواد نشتی، برف و یخ، وزن شوت پر از مواد و بار باد. پلت فرم کار کردن اطراف شوت باید برای تحمل کارهای تعمیراتی به اندازه کافی استحکام داشته باشد.
شوت های انتقال باید برای راحتی حمل و نصب چند تکه ساخته شوند. همچنین برای سیستم های اصلاحی، مقاطع شوت باید متناسب با بازشوهای موجود باشد.
در ساخت شوت باید برای جلوگیری از نواقص سطح دقت شود، وگرنه موجب مختل شدن جریان و بی اثر شدن مهندسی دقیق خواهد شد. اختلاف 3 mm± یا 1.8 in ممکن است مشکلاتی در تطبیق قطعات لاینر یا تنظیم شوت با نوار ایجاد کند. سرمایه گذاری در ساخت دقیق شوت، با راندمان بهتر، تعمیرات نگهداری ساده، و کاهش نشت مواد چند برابر برمی گردد.
علیرغم بهترین عزم در طراحی شوت، مواردی هست که مواد داخل شوت جمع خواهد شد. مواد با رطوبت بالا ممکن است به دیواره ها چسبیده یا حتی هنگام زمستان یخ بزند. عملیات پیوسته ممکن است مواد را روی دیواره فشرده تر کند، مواد بیشتری جمع شود و در نهایت شوت مسدود شود. هنگام طراحی شوت، عاقلانه است که امکانات نصب تجهیزات کمک کننده جریان flow-aid مثل ویبراتورها یا دمنده های هوا لحاظ شود.
دسترسی شوت
یک شوت محصور باید دریچه هایی برای بازرسی چشمی و درب هایی برای ورود کارگر داشته باشد و باید مسیر تمیزی برای رسیدن کارگر به این نقاط وجود داشته باشد. دریچه های بازرسی، مثل درب های دسترسی لولایی، باید به دور از جریان مواد نصب شود، بگونه ای که پرسنل بتوانند حرکت مواد را مشاهده کرده و سایش را بازرسی کنند.
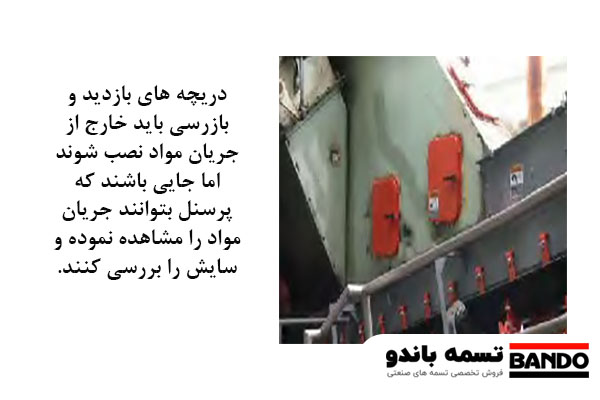
باید توری یا حفاظ برای محافظت کارگران هنگام بازدید جریان مواد از نقاط گلوگاه و اجزای دورانی درنظر گرفته شود. دریچه ها باید مقاوم به خوردگی و درزبند غبار باشند. موانع ایمنی برای جلوگیری از فرار مواد از شوت و رسیدن دست پرسنل به جریان مواد باید درنظر گرفته شود.
اغلب پیش بینی روشی برای دسترسی به تعویض لاینرهای داخل شوت یا تعمیر تمیزکن های نوار فراموش می شود. درنظرگرفتن الزامات تعمیرات آتی بویژه برای شوت های کوچک برای ورود پرسنل مهم است. یک روش تعمیرات ساخت شوت چند-تکه برای دمونتاژ آسان است. برای مطالعه بیشتر می توانید مقاله نگهداری نوارنقاله و تعمیرات کانوایر را مطالعه نمایید.
مشخصات نوعی در طراحی شوت ها
- جهت
بطور کلی طراحی شوت انتقال باید به گونه ای باشد که مواد را درجهت نوار دریافت کننده و مرکز آن هدایت کند.
- ارتفاع ریزش
ارتفاع ریزش از سیستم تخلیه به کانوایر دریافت کننده باید حتی الامکان کوتاه باشد و در ضمن فضای کافی برای نصب و تعمیرات نگهداری تجهیزات نیز فراهم شده باشد.
- سرعت
مواد باید با سرعت برابر با کانوایر دریافت کننده تغذیه شود.
- شیب
شوت انتقال باید به اندازه کافی شیب داشته باشد تا مانع غلت خوردن بیش از حد مواد بعد از برخورد با کانوایر دریافت کننده شود، چون می تواند باعث افزایش تولید غبار و خرابی ضربه شود.
- حجم
حجم شوت ریزش باید حداقل 4 برابر جریان مواد باشد. مقطع انتقال باید به اندازه کافی بزرگ باشد تا محفظه ای برای حداقل کردن جریان هوا بوجود آورد.
مباحث پیشرفته در طراحی شوت
در ادامه به شرح مباحث پیشرفته تر در مورد عرض شوت و محاسبه زاویه کنج می پردازیم.
عرض شوت
عرض نوار 1200 mm یا 48 in و زاویه تغاری 30- درجه است. عرض شوت پیشنهادی چقدر است بگونه ای که شوت با اسکرت منطبق باشد؟
قاعده 2/3 کتاب سِما عرض 800 mm یا 32 in را به دست می دهد. روش دیگر برای تعیین فاصله بین اسکرت ها بر اساس مقدار فاصله لبه لازم برای درزبندی مؤثر و تطابق با انحرافات نوار می باشد. برای یک نوار عرض 1200 mm یا 48 in و زاویه تغاری 30- درجه عرض اسکرت توصیه شده برابر 894 mm یا 35.2 in است. اختلاف بین روش سِما و لبه نوار belt-edge برای نوار های خیلی باریک و خیلی عریض قابل توجه است.
محاسبه زاویه کنج در طراحی شوت
یک شوت جدید با حداقل زاویه کنج 60- درجه موردنیاز است. زاویه دیواره کناری 75- درجه و دیواره پشتی 60- درجه انتخاب شده است. چون این مقادیر در محدوده توصیه شده است. این رابطه را می توان برای چک کردن طراحی شوت به کار برد.
در این مثال زاویه کنج حدود 57- درجه به دست می آید. بنابراین طراح برای رعایت حداقل زاویه 60- درجه باید مجددا به طراحی شوت بپردازد. اگر زاویه ها به 65- درجه و 75- درجه تغییر کند زاویه کنج 61- درجه خواهد شد که برای برقراری جریان به اندازه کافی شیب دارد.
باید توجه کرد که زاویه کنج هیچوقت بزرگتر از کوچکترین زاویه دیواره کناری و پشتی نمی شود. طراحی شوت با انتخاب زوایای مختلف دیواره پشتی و محاسبه زاویه کنج رفت و برگشتی خواهد شد. اگر زاویه کنج در طراحی شوت مناسب نباشد، زوایای دیواره مختلف باید انتخاب شود و زاویه کنج برای زوایای انتخاب شده، محاسبه شود. این فرایند تکرار می شود تا زوایای دیواره با هندسه موجود متناسب شود و زاویه کنج در محدوده صحیح بر حسب مواد قرار گیرد.
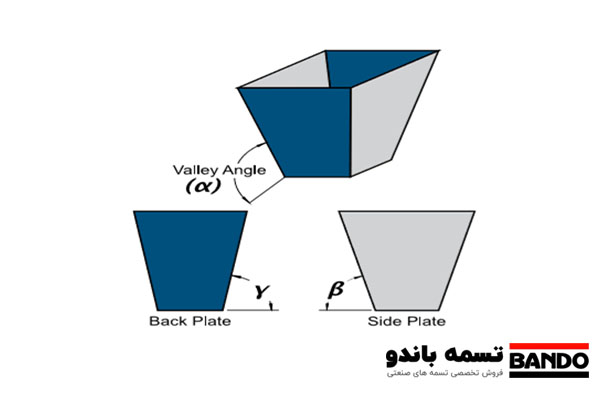
کار شوت
در صورت طراحی شوت انتقال به طریقی درست، روش ایمنی برای انتقال مواد از یک ارتفاع به ارتفاع دیگر خواهد بود، با حداقل مواد نشتی و کمترین تعمیرات. وارد کردن مطالب بحث شده در این مقاله به نقشه ها، برای هم طراح و هم کاربر نهایی ابزاری مناسبی به دست خواهد داد تا عملکرد عملی شوت و چگونگی طراحی شوت یا اصلاح شوت برای عملکرد بهتر را متوجه شوند.
منبع: کتاب FOUNDATIONS ترجمه معصومه امین.